La progettazione delle aree EPA e dei sistemi di protezione ESD in genere, non può dissociarsi dai requisiti indicati dalle normative. Sebbene non cogenti quali quelle di sicurezza, il loro recepimento è fondamentale essendo determinato dal mercato, ma soprattutto dal buon senso che deve necessariamente veicolare le strategie aziendali.
La progettazione di aree EPA e dei sistemi di protezione ESD debbono incontrare i requisiti della normativa CEI EN 61340-5-1 mentre i sistemi utilizzati per la movimentazione debbono riflettersi nelle prescrizioni indicate dalla normativa CEI EN 61340-5-3. In aggiunta ai modelli indicati da tali normative si dovrà necessariamente considerare il modello CBE (Charged board Event) principalmente legato a manipolazioni automatiche, flussi di aria elevati ed anche ad interferenze di isolanti (inclusa l’induzione). Da non trascurare inoltre la vulnerabilità ad eventi ESD di un prodotto finale il quale deve essere in grado di superare i test di immunità ESD i quali simulano condizioni avverse potenzialmente presenti in applicazione ed anche shock elettrici associabili alle fasi di connessione con altri apparati (plug – unplug).
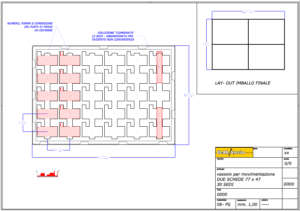
Le scelte da adottare debbono essere strutturate nell’ottica del “robust design” al fine di limitare al minimo l’errore umano e a tal proposito diviene fondamentale la presenza di un coordinatore oppure di un “program manager ESD” il quale dovrà garantire l’idoneità dei processi produttivi in linea con lo stato dell’arte e con l’evoluzione tecnologica.
All’interno di un’organizzazione, infatti, l’efficacia di un programma ESD è tassativamente associata alla condivisione inter-funzionale ed i punti fondamentali risultano essere la formazione, la disciplina, la competenza in sede di progettazione e la certificazione.
Le normative
La normativa CEI EN 61340-5-1 del 2016 oltre a definire i criteri atti a garantire il massimo potenziale di 100 Volt (HBV – Human Body Voltage) all’interno di aree protette, stabilisce un livello max di 35 volt su conduttori isolati da terra (storicamente definito Machine Model) e di 200 volt di CDM (charged device model).
I modelli HBM e MM sono normalmente gestiti attraverso il collegamento equipotenziale che consente l’interazione tra i vari conduttori, mentre il modello CDM è determinato quasi sempre dalla presenza di isolanti nel processo (non gestibili attraverso i sistemi passivi).
Essendo il componente sensibile al potenziale dell’isolante con cui entra in intimo contatto, l’eventuale scarica andrà a manifestarsi nella direzione del corpo (solitamente a terra) con cui esso verrà in contatto.
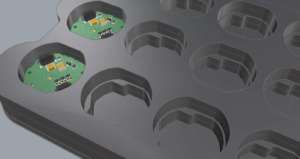
Nello specifico la carica accumulata dal dispositivo si distribuisce nei suoi elementi strutturali e quando uno dei suoi terminali viene a contatto con un corpo estraneo, il flusso di corrente che si genera segue dei percorsi difficilmente prevedibili, rendendo difficile la progettazione di adeguate strutture circuitali di protezione.
La protezione da eventi CDM durante la manipolazione, oltre ad un’accurata gestione degli isolanti (banditi quando non necessari) non può prescindere dall’impiego di sistemi attivi (ionizzatori) che sono indispensabili in postazioni ove sono presenti isolanti di processo, ma anche in presenza di conduttori isolati da terra (parti mobili di macchine e ventose).
L’avvento massivo di polimeri nella realizzazione di prodotti e ambienti produttivi (isolanti quali silicone, PE, ABS PVC, PET) ha esposto maggiormente assiemi e componenti sensibili a ESD che in molte circostanze risultano intimi, oppure accoppiati ad isolanti necessari al processo o parte integrante di un prodotto finito.
Le normative IEC 61340-5-1 e 61340-5-3, di fatto da considerare norme di sistema, si avvalgono di metodi di prova per condurre i test di qualifica; in merito alle verifiche (monitoraggio sull’efficienza dei sistemi in uso) sono invece stati emessi recentemente due rapporti tecnici (IEC T.R.) i quali indicano metodi di prova semplificati per le verifiche periodiche quali IEC 61340-5-5 (packaging) e 61340-5-4 (ESD protective item).
Oltre ai modelli sopracitati, è ormai da tempo in fase di studio il modello CBE (Charged Board Event); è infatti possibile che nelle fasi di manipolazione (principalmente automatiche) si possa danneggiare un PCBA. Di fatto il modello CBE, in un processo di assemblaggio, si manifesta spesso attraverso una scarica da un PCBA carico e nell’occasione determina uno stress elettrico ai suoi componenti.
La gestione del modello CBE è da intendersi una sfida nell’elaborazione di un programma di controllo ESD a causa della grande varietà dei processi di assemblaggio, senza trascurare la progettazione del prodotto stesso (robust design). In aggiunta non si debbono escludere nelle valutazioni a cura del responsabile ESD sia le sonde che le fixtures utilizzate per i test.
A tal proposito a complemento delle prescrizioni della norma IEC 61340-5-1, un programma ESD di controllo efficace deve:
- localizzare i passaggi critici di una linea di assemblaggio;
- definire la soglia massima di potenziale a ESD ammesso (taylored vs prodotto);
- fornire protezione sufficiente ad eliminare il rischio di eventi ESD durante tutte le fasi di processo incluso il test.
Come indicato dalla normativa CEI EN 61340-5-1, in merito alla definizione di area protetta si intende: un banco, un magazzino, un’area di lavoro, una postazione di assistenza sul campo, una stazione di lavoro oppure una apparecchiatura (ad esempio una P&P).
Il responsabile del programma ESD sia nell’ambito della progettazione di aree EPA, ma anche in quello della scelta e della realizzazione di adeguati sistemi per la movimentazione, deve necessariamente considerare i modelli sopracitati; è pertanto possibile affermare che tali attività sono da intendersi le fasi più importanti per poter assicurare la protezione da eventi ESD indesiderati.
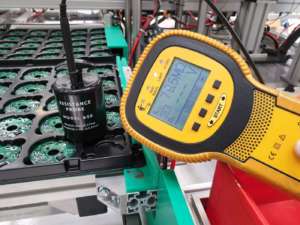
Un aspetto fondamentale è legato all’impiego di materiali idonei atti a garantire l’efficienza dei sistemi di protezione, i quali debbono ottemperare alle prescrizioni della IEC 61340-5-1 sia nelle condizioni critiche (UR 12%) che attraverso il tempo. Il “design robusto” prevede l’impiego di prodotti che mantengano le loro caratteristiche per tutta la loro vita.
L’imballaggio
In generale l’imballaggio è necessario per proteggere le parti contenute da guasti fisici ed ambientali nelle fasi produttive, nella movimentazione e nell’immagazzinamento. Per componenti ed assiemi elettronici, la sua funzione è quella di proteggere prodotti sensibili a ESD da scariche e campi elettrostatici.
A complemento della normativa CEI EN 61340-5-3 che fornisce indicazioni in merito alla qualifica, vi è la normativa CEI EN 61340-5-5 che indica i metodi da applicare nelle fasi di verifica e monitoraggio.
La scelta del tipo di imballaggio, oltre ad essere vincolata dalla applicazione (corrosione, contaminazione, umidità, fenomeni elettrochimici etc) è una prerogativa fondamentale per garantire la protezione necessaria nelle fasi di trasporto e stoccaggio; inoltre introduce frequentemente un significativo risparmio sul costo del prodotto finito.
Limitandoci a prestazioni inerenti costi e tempi è infatti possibile affermare che per gli imballi interni (EPA) si debbano privilegiare i tempi di scarico e carico, mentre per la movimentazione tra EPA diviene necessario privilegiare le quantità contenute, sviluppandoli con dimensioni che siano sottomultipli di euro pallet.
Da non trascurare inoltre la contaminazione (impiego in camere bianche) che deve necessariamente veicolare la scelta verso imballi a base polimerica: termoformati, vassoi realizzati ad iniezione, scatole in PE e shielding/barrier bag.
Un’attenzione particolare deve essere indirizzata ai costi, in questo caso per movimentazioni a “volumi” è possibile affermare che per gli imballi a perdere si debba privilegiare l’impiego di cartone avana (low charging) complementare a buste shielding; spesso il cartone avana è utilizzato impropriamente per contenere PCBA posti all’interno di buste dissipative.
Negli imballi riutilizzabili la scelta non può prescindere dall’impiego di termoformati conduttivi (spesso integrati con newbox in polipropilene), sovrapponibili se contengono schede ed impilabili quando sono vuoti, che riducono al minimo i costi di trasporto attraverso una semplice rotazione di 180°.
Movimentazione tra EPA
All’interno di EPA, per la movimentazione di ESD, è importante disporre di imballi conduttivi, statico dissipativi ed anche schermanti; nelle UPA invece è mandatorio disporre di imballi schermanti. La schermatura si ottiene attraverso due grandezze fondamentali quali lo spessore e la resistenza superficiale. Nello specifico più è bassa la resistenza (metallizzazione) e meno è necessario lo spessore. Per gli imballi multipli le due opzioni maggiormente in uso sono le buste shielding ed i termoformati mentre per gli imballi singoli è il cartone schermante (safe shield).