Le soluzioni integrate KEBA, il ruolo dell’IA e della tecnologia di controllo avanzata, stanno migliorando la precisione e l’efficienza delle macchine per stampaggio a iniezione elettriche e ibride.
Nelle macchine per stampaggio a iniezione elettriche e ibride, i movimenti non sincronizzati causano danni costosi. In questo articolo KEBA spiega come le sue tecnologie di controllo e l’assistente IA integrato consentono la sincronizzazione precisa che migliora l’efficienza e protegge i macchinari.
Nella realtà pratica non esiste solo un unico asse per il controllo di un determinato movimento poiché a seconda di potenza e/o coppia necessarie, vengono impiegati numerosi moduli di azionamento multi assiali, come nel caso di una macchina per stampaggio a iniezione elettrica dotata di due servoazionamenti monoasse e due motori. Per far funzionare i motori, erogare la stessa tensione non equivale a uguale movimento poiché vi è sempre uno scostamento seppur lieve fra le velocità. Ciò può causare costosi danni poiché l’eccessiva pressione esercitata su di un solo lato può produrre danni meccanici ai vari componenti: stampi, espulsori e iniettori, ma anche controllo e azionamento perché il movimento può deviare all’indietro e creare danni non solo al motore stesso, ma anche l’elettronica (fig. 1). E cruciale quindi ottenere comunicazioni e sincronizzazione rapide fra dispositivi: evitare danni ai componenti equivale a evitare fermi macchina indesiderati.

Tecnologia di controllo a reazione rapida “3-in-1”
La rapida comunicazione e reazione tra dispositivi è cruciale e consente un controllo efficace e ad alta velocità del bilanciamento della posizione, oltre che al controllo di altri processi. Il tempo morto è la quantità di tempo richiesta affinché una variazione dell’input determini una modifica dell’output tramite una funzione di controllo rapido.
Un PC industriale impiega di solito tre tick di ciclo per leggere, calcolare e inviare una risposta (fig.2). Invece, con la funzione di controllo a reazione rapida, i controller KEBA, completano lettura, calcolo e risposta in un solo ciclo di controllo (fig.2). A inizio frame, il controller legge i segnali di input per poi calcolare immediatamente i valori di output e scriverne i relativi segnali alla fine del frame di scansione. Questa funzione è compatibile con EtherCAT e con gli IO della scheda IO e influisce sul controllo della pressione nel controller migliorando la comunicazione tra azionamenti. La minimizzazione del tempo morto è indispensabile per migliorare la qualità del processo, ottimizzare le prestazioni della CPU e garantire i migliori risultati minimizzando il jitter.
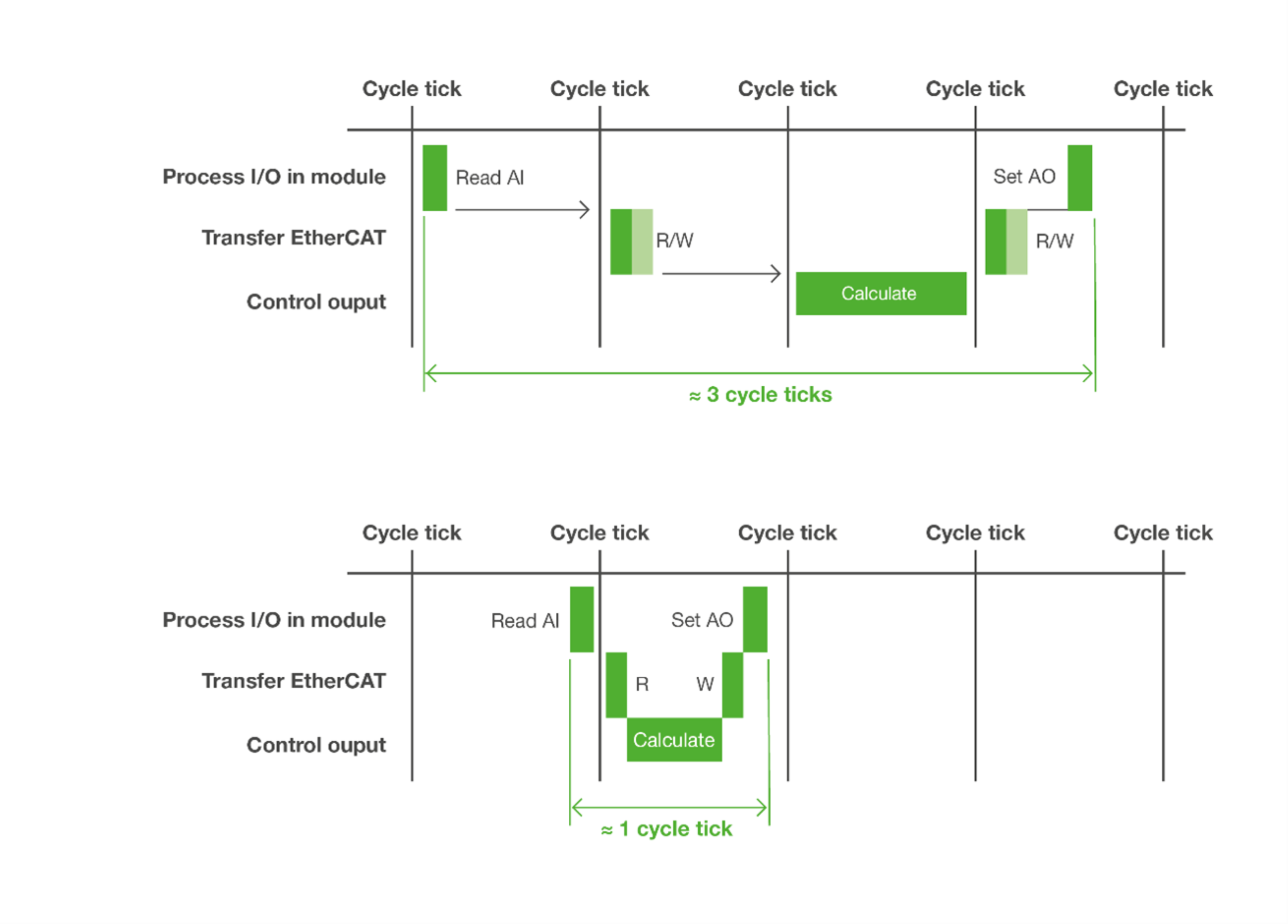
Sincronizzazione e controllo con qualsiasi tipo di azionamento
Valori come controllo della pressione o controllo per compensazione della posizione, possono essere effettuati sul controller. Per molto tempo ciò ha rappresentato un importante standard di riferimento nel controllo di processo nello stampaggio a iniezione e tuttora è la soluzione all'avanguardia per le macchine idrauliche. A confronto, le nuove soluzioni che integrano il controllo pressione e posizione nel servoazionamento offrono tempi morti ridotti grazie a funzioni di controllo rapido ma anche maggiore rapidità di controllo della pressione e il vantaggio di agire direttamente sull'azionamento in reazione agli errori. Questi vantaggi sembrano essere validi motivi per cui molti OEM stanno adottando la nuova tecnologia.
Ci si potrebbe chiedere se gli assistenti al controllo pressione e bilanciamento della posizione di KEBA funzionano anche con azionamenti di terze parti. La risposta è si anche se la combinazione di controller, servoazionamenti come anche i motori KEBA offre i vantaggi illimitati grazie ad hardware e software provenienti da un unica fonte.
Attraverso i controlli di pressione e del bilanciamento della posizione sull'azionamento, l’assistente AI KePlast Position Balance Control sincronizza tutti i movimenti richiesti in relazione all'applicazione. Durante il set-up si effettua una distinzione fra movimenti per stabilire quali debbano essere controllati (ad esempio i movimenti dell’espulsore, dello stampo o dell’iniezione) poiché ognuno ha requisiti differenti. I movimenti di iniezione, ad esempio, generalmente richiedono due azionamenti monoasse per il controllo ad alta pressione. Il movimento dello stampo potrebbe invece essere gestito con un solo controller a doppio asse perché non sono previste coppie molto elevate.
Il controllo a reazione rapida e l'assistente AI per il controllo del bilanciamento della posizione KePlast di KEBA funzionano efficacemente su qualsiasi servoazionamento, a 1, 2 o 3 assi e anche su tutti i servocontroller KeDrive D3.
I vantaggi per l'utente finale offerti dall’AI KePlast Position Balance Control
La perfetta comunicazione incrociata durante il controllo pressione e bilanciamento della posizione si svolge in sette step (Fig.3):
- Il controller invia all'asse master il valore di pressione target mentre il modulo AI invia quello di pressione corrente.
- In base a questi valori prestabiliti e al controllo della pressione sull'azionamento, si calcola la velocità di riferimento.
- L'asse master confronta la propria posizione attuale con quella corrente dell'asse slave.
- Dai valori di posizione di Master e Slave, viene calcolata la correzione per il riferimento della velocità determinato dal controllo pressione.
- La correzione, in relazione al valore di posizione, viene aggiunta per un asse e sottratta per l'altro.
- L'asse master invia successivamente il setpoint #1 calcolato al motore 1 e il setpoint #2 all'asse slave che lo inoltra al motore 2.
- Con questo sistema viene controllata correttamente la pressione e mantenuta a zero la differenza di posizione fra motori.
Va ricordato che è necessaria la presenza di un sensore di pressione sull'asse master.
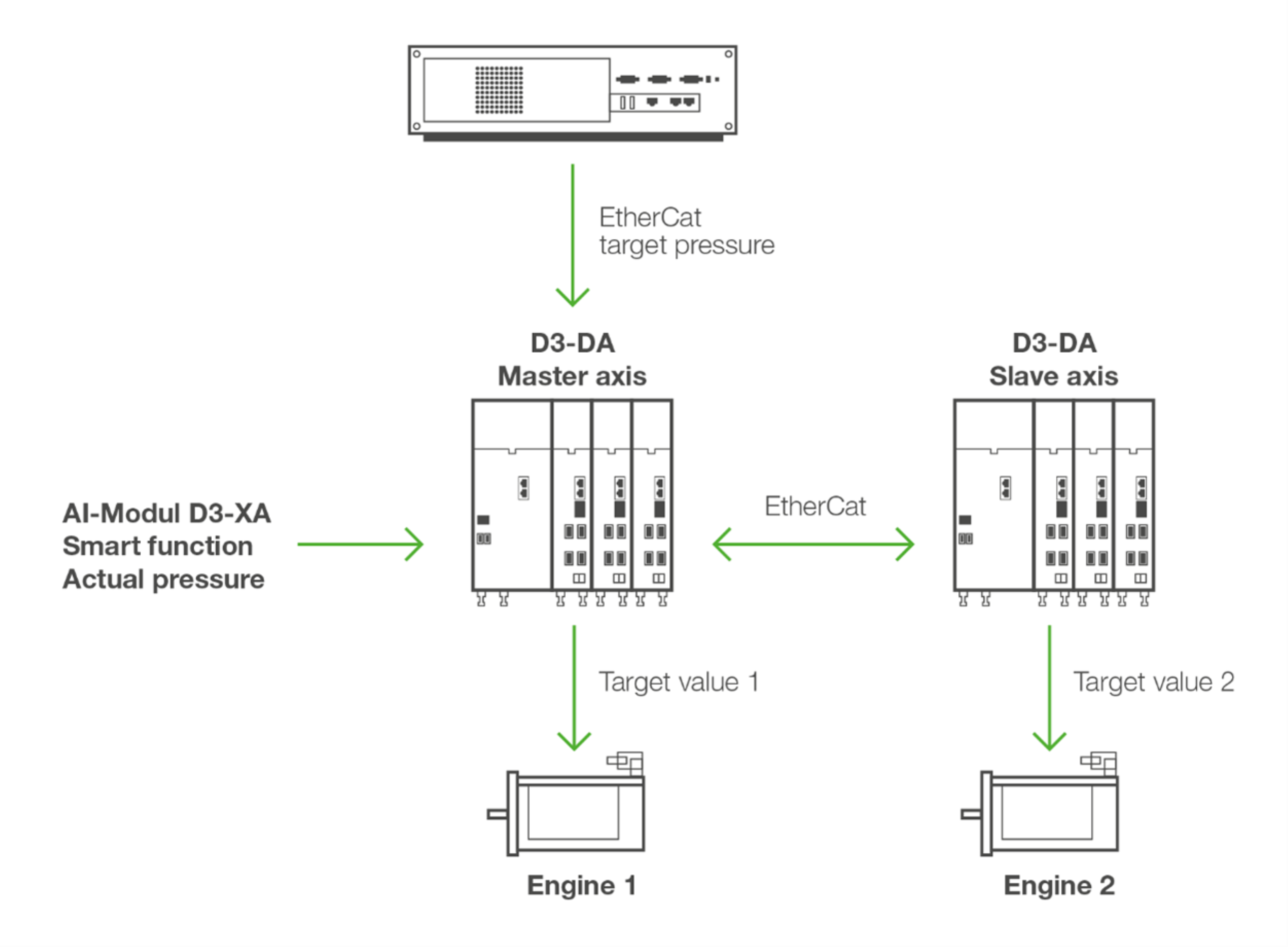
L’applicazione illustrata offre quindi numerosi vantaggi. Per primo, il controllo pressione avviene sull'azionamento in 125 µs, valore che è considerato di riferimento per la durata del ciclo. Secondo, l'azionamento reagisce direttamente nel caso di errore, evitando i conseguenti danni e minimizzando i tempi di inattività. Con il controllo a reazione rapida, i tempi morti causati da comunicazioni incrociate sono anch'essi minimizzati perché l'intero ciclo del controller richiede un solo tick di ciclo invece dei tradizionali tre.